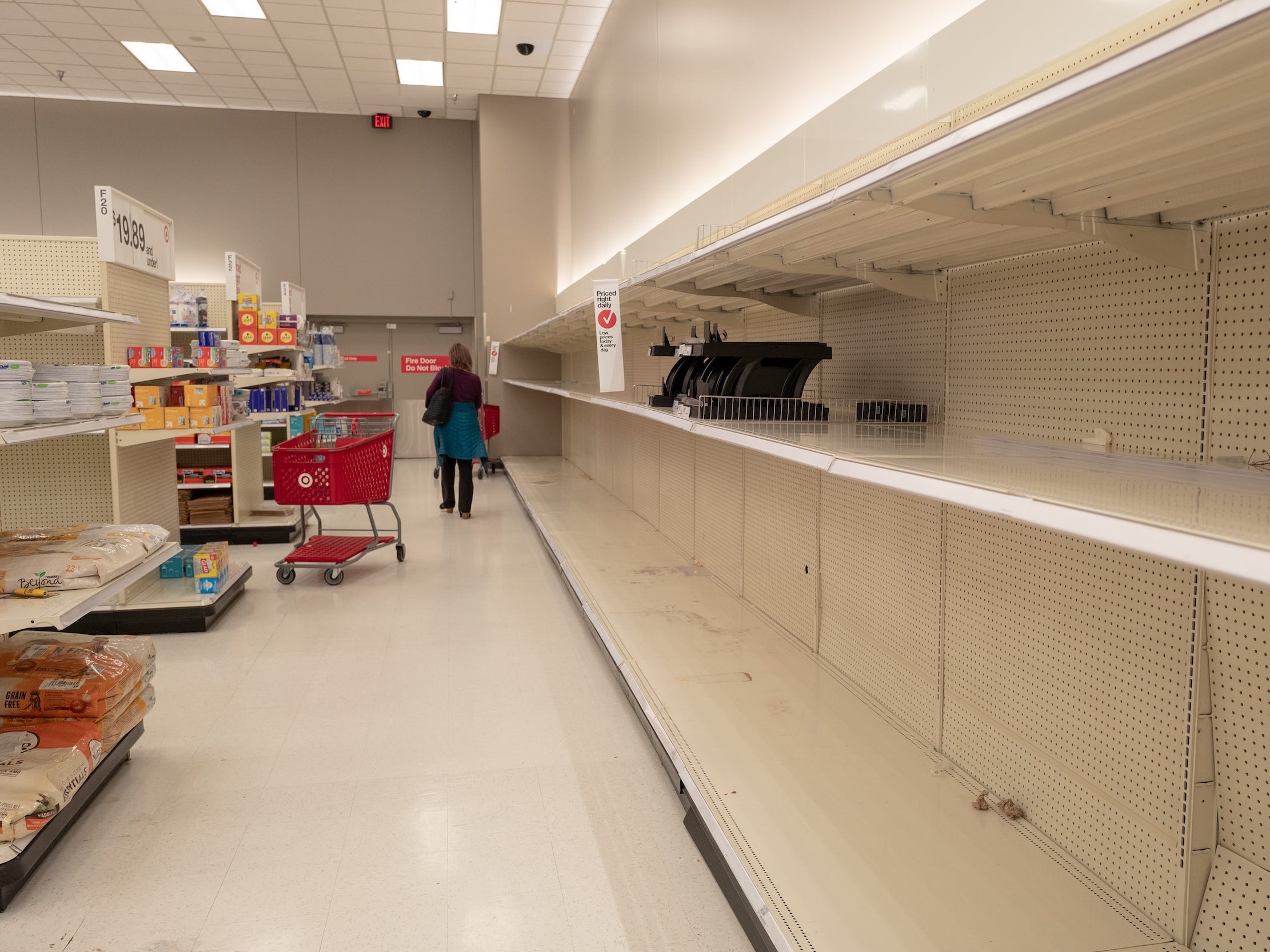
Smith Collection/Gado/Getty Images
- The supply-chain crisis is the result of COVID-19 disruptions paired with a boom in demand.
- Shortages of workers, equipment, and space have only made the issue worse.
- Here's everything you need to know about what's causing the supply-chain chaos.
America seems to be running out of everything.
Supply-chain bottlenecks caused record shortages of everyday products from household goods and electronics to cars, food, and raw materials.
For shoppers, empty shelves can be jarring, spurring panic-buying sprees. It's often the first sign people see that something may be wrong with the global supply chain. But, shortages are typically indicators of issues that have plagued the industry for months.
"At this point, shortages are guaranteed," Jonathan Gold, vice president of supply chain policy at the National Retail Federation, told Insider. "… We've been warning consumers to manage their expectations for the holiday shopping season for months now. The fact of the matter is the supply chain is stretched to its limit from end-to-end."
The supply chain didn't recover from COVID-19
In 2020, coronavirus shutdowns wreaked havoc on the global supply chain. Since, lingering virus-mitigation measures continue to limit efforts to return the supply chain to pre-pandemic levels.
Several industry players limited worker levels due to fears of the further spread of COVID-19 within the workplaces. In China, port terminals temporarily shuttered as a result of the country's COVID-19 zero-tolerance policy, spawning backlogs at some of the world's largest ports.
"From an economic perspective, it's sort of like a game of musical chairs," former US trade negotiator Harry Broadman told Insider, pointing to efforts in the US to compete with 24/7 operations at Asian ports. "The world economy is out of sync because parts of it were forced to go offline when the pandemic started and getting all the industry players back in line at the same time is near impossible."
Demand is soaring
Demand grew so rapidly in the past two years that it's equivalent to about 50 million new Americans joining the economy, Gold told Insider.
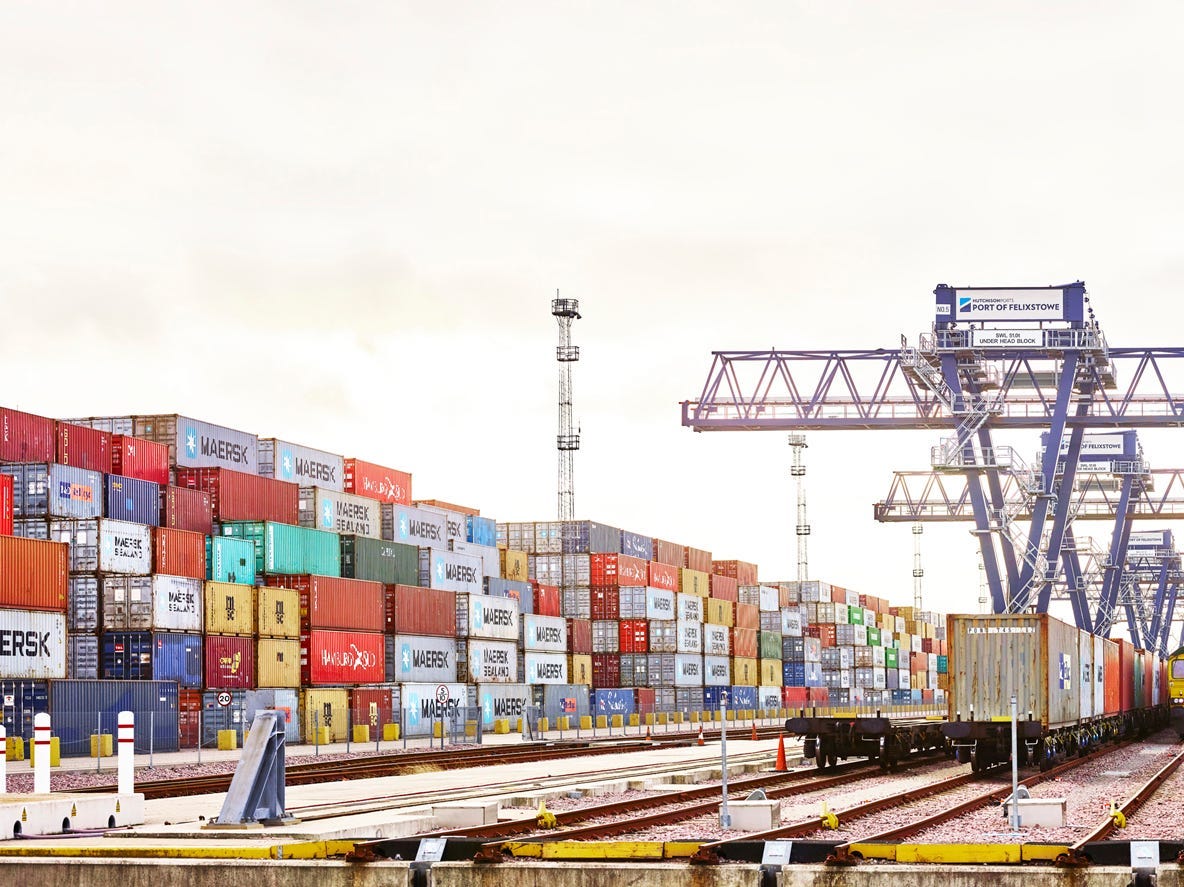
Courtesy of the Port of Felixstowe
"All parts of the supply chain, most of which are built on 'lean' principles (no slack, little redundancy, from truck drivers to inventory in warehouses), were not prepared for this increase," Pelli told Insider. "While consumer demand can increase in a matter of months, it takes more time to increase port capacity, build warehouses, hire employees, etc., to meet that demand."
Shortages make it difficult to keep up
Ports, warehouses, and trucking companies are processing more goods than ever while combatting a series of crushing shortages, including workers, equipment, and space.
A lack of chassis and shipping containers has made it even more difficult to transport goods.
Most notably, the national labor shortage has left warehouse companies scrambling for employees and key US ports working with limited manpower.
Two of the largest US ports saw a 30% increase in the amount of goods going through them while processing the cargo with 28% fewer workers. In July, the US Labor Department reported that the warehouse industry had a record 490,000 job openings. Meanwhile, the trucking industry has a shortage of over 80,000 drivers.
With fewer workers to process the goods, shipping yards and warehouses are running out of space, making it increasingly difficult to organize the output of goods to their final destinations.
No end in sight
While the record backlog at Southern California ports represents the most eye-grabbing aspect of the supply-chain crisis, every leg of the industry is in chaos, RBC analyst Mike Tran told Insider. Last week, Moody Analytics warned there will be "dark clouds ahead" for the supply chain.
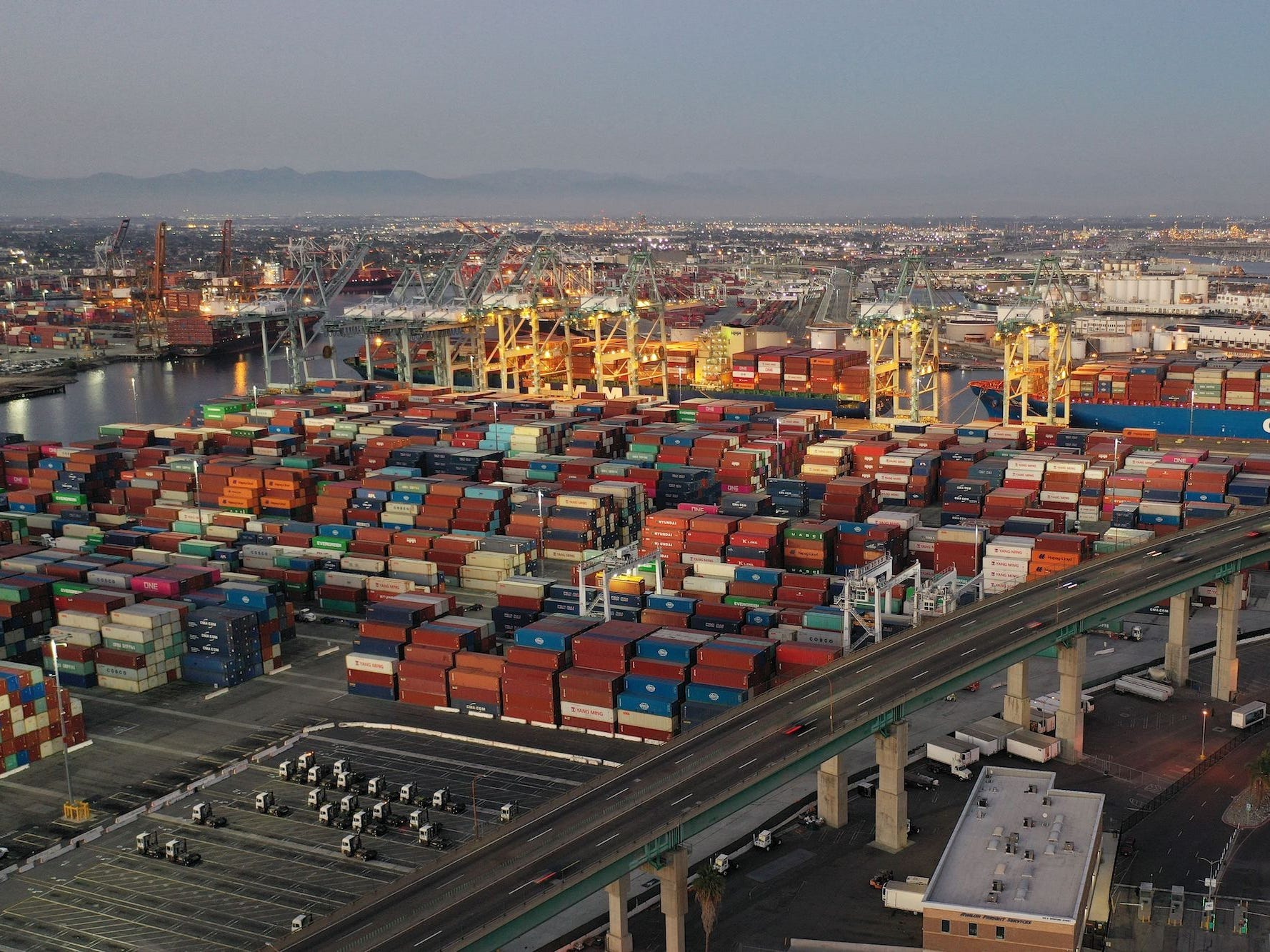
The only realistic near-term solution would be a cut back on consumer spending, though the prospect seems unlikely.
Experts predict the disruptions will continue well into 2023, despite efforts from the government to mitigate the issue.